WELD INSPECTION & TESTING
Swantest can provide a comprehensive array of weld inspection and consultancy services across the UK.
All our welding inspectors and consultants are fully trained and qualified to CSWIP and PCN standards and are skilled in maintaining welding quality to the latest standards and regulations.
Responsible welding co-ordinator (RWC):
Swantest can act as your companies RWC within all your welding related activities and manufacturing processes. A good weld quality management system is an essential part of a production and manufacturing procedure.
Swantest will enable you to ensure that the highest standards of quality are maintained and identify specific areas of welding process that requires attention. Each management system can be tailored to suit your company's needs and requirements for your current and future developments.
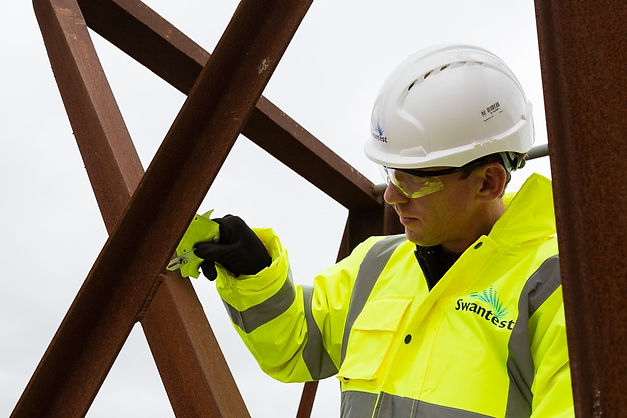
Visual Weld Inspection
Swantest have a team of qualified visual weld inspectors who can carry out onsite inspections. One element critical in a weld quality system is the external examination of the weld.
Fabricators rely on radiography or ultrasound to check weld integrity. However, defective welds can often be identified through visual inspection. Visual weld inspection has the benefit of being able to be carried out on site, with minimal production delays and providing immediate feedback to welders and designers.
Our weld inspectors can be on site to check welds as soon as they have been completed. Identifying any defect this early can have vast time and cost savings.
MPI (Magnetic Particle Inspection)
MPI (Magnetic Particle Inspection) is an NDT technique designed to detect surface indications in ferromagnetic materials. Surface cracks in welds, castings and forgings often appear, however, they are not visible to the human eye. Cracks can and will cause major integrity problems to installations.
Why MPI?
Magnetic particle inspection is a fast, extremely sensitive, and low-cost method for weld surface inspection.
MPI is most commonly be used on new and existing structural welds in order to identify and highlight any defects or stresses in the weld material and adjacent areas.
Ultrasonic Testing (UT)
Ultrasonics or ultrasonic testing (UT) involves production of high frequency sound waves for the purpose of detecting imperfections in a welds and metals. Sound energy is introduced via a probe transducer and propagates through the material. When there is a discontinuity (i.e. a crack or lack of fusion) in the wave path, part of the energy will be reflected back to the probe from the flaw surface. The reflected wave signal is transformed into an electrical signal by the transducer and is displayed in the form of echoes.
Swantest PCN level 2 technicians can detect discontinuities and flaws within the material, characterize and take precise dimensional measurements. Swantest use the latest Ultrasonic testing equipment can not only find the flaws, but also estimate their near-accurate shape and size located even at the highest penetration depths.
UT forms part of a robust QA process on site and workshop welds. This type of inspection can be utilized to locate existing defects in various materials and components. These include welds in steel plate or pipe, continuous castings, tubular materials, composites, and many more. Our Inspection procedures comply with the latest British and European Standards, AWS, ASME, API and ISO codes.